Value Engineering: Definition and 4 Key Principles
The definition and four key principles to the secret of effective cost-cutting in construction
February 20, 2025
7
min read
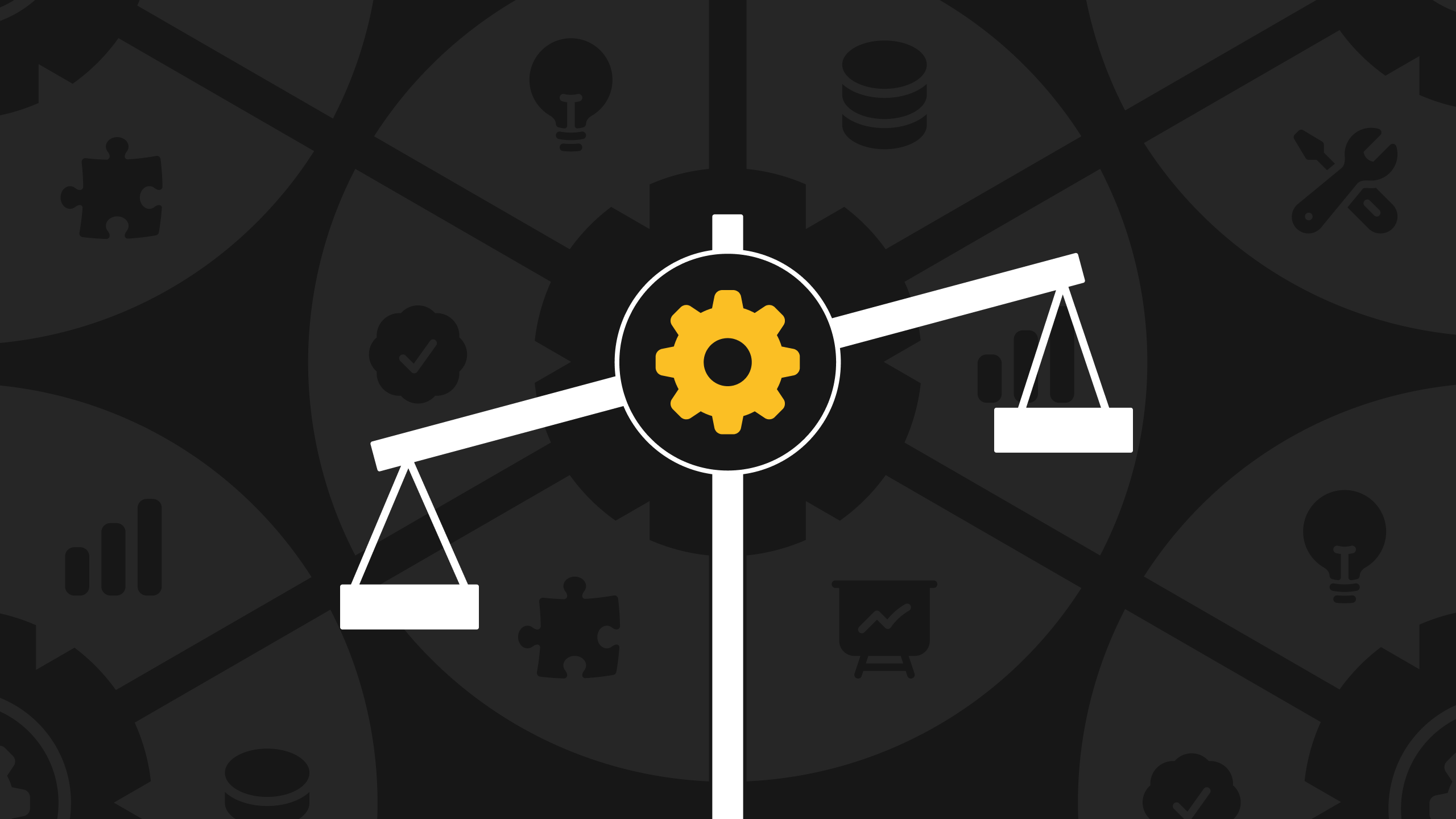
Introduction
Value Engineering is unfairly misunderstood as a cost-cutting tactic in construction. You have to admit the term itself sounds like a type of sales-speak euphemism: “Let’s roll up our sleeves and do some ‘value engineering (wink).’” The wink and quotes were for effect, but you get the point.
Far from simply reducing budgets in a slimy way, VE is a structured approach designed to optimize project value by balancing essential functionality with efficient resource usage.
By applying a clear methodology and fostering an environment of collaboration, VE can transform everything from design choices to material selection—ultimately leading to significant, yet sustainable, cost savings. Cha-ching, respectfully.
Definition
Value Engineering in construction is a systematic method for analyzing a project’s components, functions, and costs to identify cost-saving or value-enhancing opportunities.
Unlike no holds barred budget-cutting, it involves optimizing design, materials, and processes to maximize functionality and quality while minimizing overall costs throughout the project’s life cycle. The emphasis here is on “quality.”
Now that we’ve defined Value Engineering, let’s explore its four key principles. Each one highlights not only how to cut costs responsibly, but also how to ensure that quality, performance, and innovation remain integral parts of the process.
The 4 Key Principles of Value Engineering
1. Function Over Cost
“Spared no expense,” John Hammond’s iconic flex from Jurassic Park, almost exactly contrasts with the ethos of Value Engineering. While Hammond glorifies limitless spending, VE zeroes in on minimizing costs strategically—always keeping the core function of each project element in mind.
The initial step involves identifying and fully understanding what each part of the project must accomplish. Only then can you explore suitable, lower-cost alternatives that maintain or even improve upon these foundational functions.
By defining each element’s essential role, teams can uncover hidden efficiencies or overlooked substitutions (“switcheroo’s” in some circles). Whether it’s swapping out a certain building material for something equally durable at a lower price, or simplifying a design to reduce unnecessary features (“style over substance,” in some circles), the goal is to preserve or enhance the project’s fundamental purpose. This principle ensures budgets are reduced where possible without losing sight of quality and performance.
2. Systematic Approach
Rather than a hasty move to slash expenses all willy-nilly, VE is executed through a series of systematic phases—such as Information, Speculation, Evaluation, Development, and Presentation. In each phase, teams collect data, analyze the design, brainstorm various improvements, assess feasibility, and present well-rounded and well-intentioned proposals. This hyper-empirical structure helps avoid scattershot decision-making and keeps everyone focused on achieving value retention above everything.
In practice, this means leveraging tools that can centralize data and decision-making. Buildr, one such option, is a preconstruction platform that offers a concrete way to capture every VE option and approved decision, making it simpler for all involved parties to stay aligned.
By adhering to a well-defined process, teams make decisions that are informed, tracked, and far more likely to yield cost-saving measures without compromising on functionality or quality.
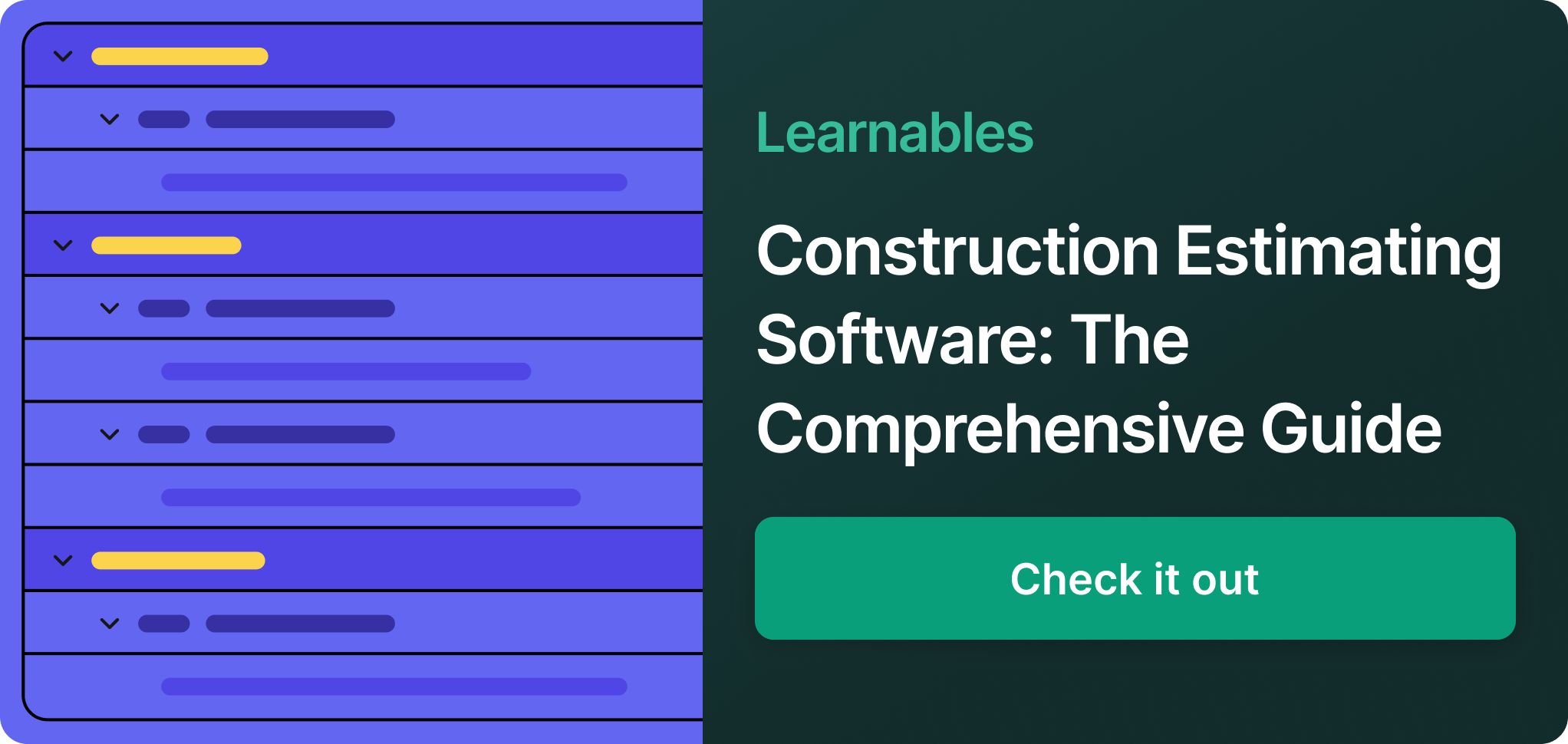
3. Stakeholder Collaboration
A successful VE initiative isn’t confined to a single discipline—it demands the input of architects, engineers, estimators, project managers, and more.
Each persona brings a unique lens: architects might suggest design tweaks that maintain aesthetic appeal while lowering costs, while cost estimators identify places for savvy budgetary optimizations. Engineers ensure that any proposed changes still meet technical requirements, and project managers keep the overall effort on track.
When these roles interact fluidly, the resulting solutions are more comprehensive and resilient. Projects that lack such collaboration often fail to spot cost inefficiencies or structural issues until it’s too late, leading to budget overruns or compromised quality. In contrast, a well-orchestrated VE process breaks down silos, unlocking the full potential of collective expertise and thereby driving better outcomes for everyone involved.
To loop back to the Jurassic Park reference earlier, it’s arguable that the park’s ultimately tragic shortcomings arose from siloed departments. You should’ve conferred more with your engineers, John Hammond!
4. Psychological Safety
Finally, psychological safety is crucial for any environment that values creativity and innovation. If team members feel inhibited or fear backlash for their ideas, you risk missing out on truly out-of-the-box solutions. Encouraging open-mindedness allows for the free-flow of unconventional thoughts that can spark major cost savings or performance upgrades.
In short, no idea is too stupid.
That said, a creative atmosphere doesn’t imply a lack of rigor. The structured phases of VE ensure every idea undergoes thorough evaluation before it’s implemented. Think of psychological safety as the engine that drives fresh thinking, and the VE framework as the guidance system ensuring that the best ideas rise to the top—ultimately serving the project’s functional goals and budgetary constraints.
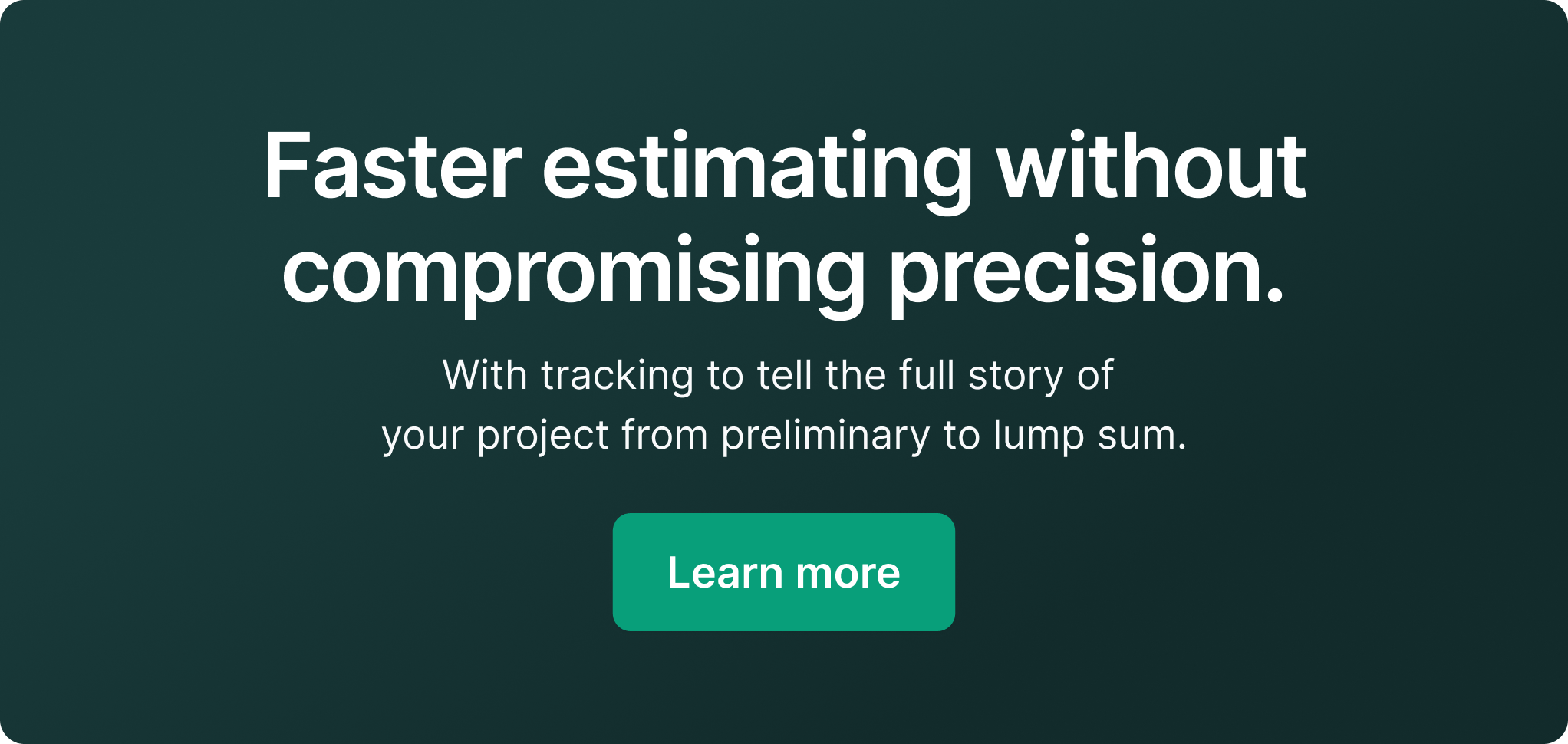
Final Thoughts
Taken together, these four principles form the backbone of an effective Value Engineering process. They guide teams to cut costs wisely, maintain or enhance quality, and foster an environment where every angle is explored for potential improvements.
By implementing VE in a thoughtful, structured way, you’re doing much more than reducing expenses. You’re maximizing your project’s potential, and on a macro scale—your business’s potential. From preserving key functions to promoting creative, cross-disciplinary teamwork, Value Engineering is a powerful strategy for delivering high-value construction projects without inflating budgets.
Stay in the loop.
Get the latest expert insights, tips, and updates on preconstruction, business development, estimating, and more — delivered straight to your inbox.
Stay in the loop.
Get the latest expert insights, tips, and updates on preconstruction, business development, estimating, and more — delivered straight to your inbox.